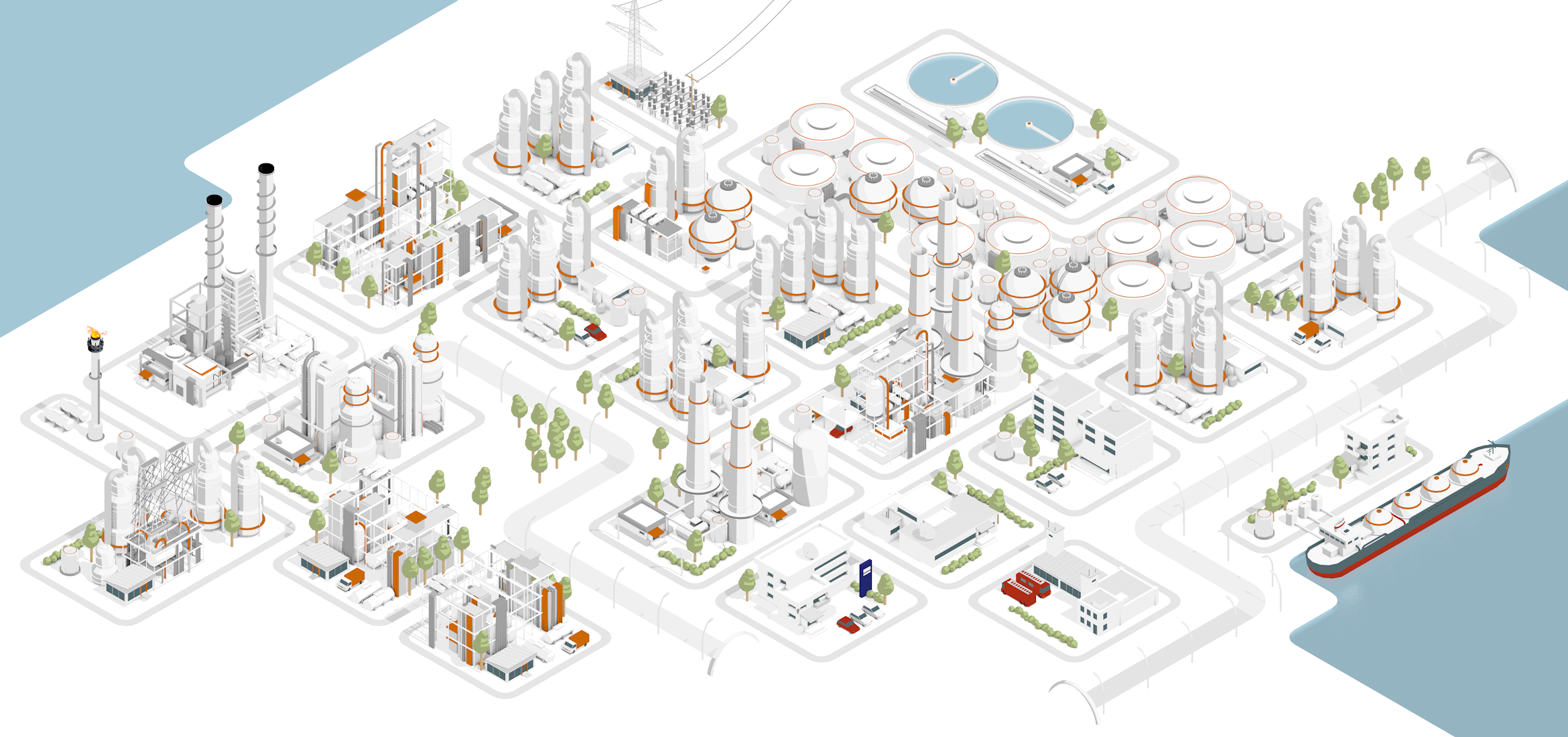
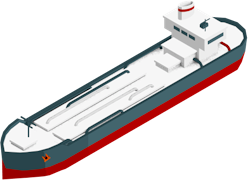


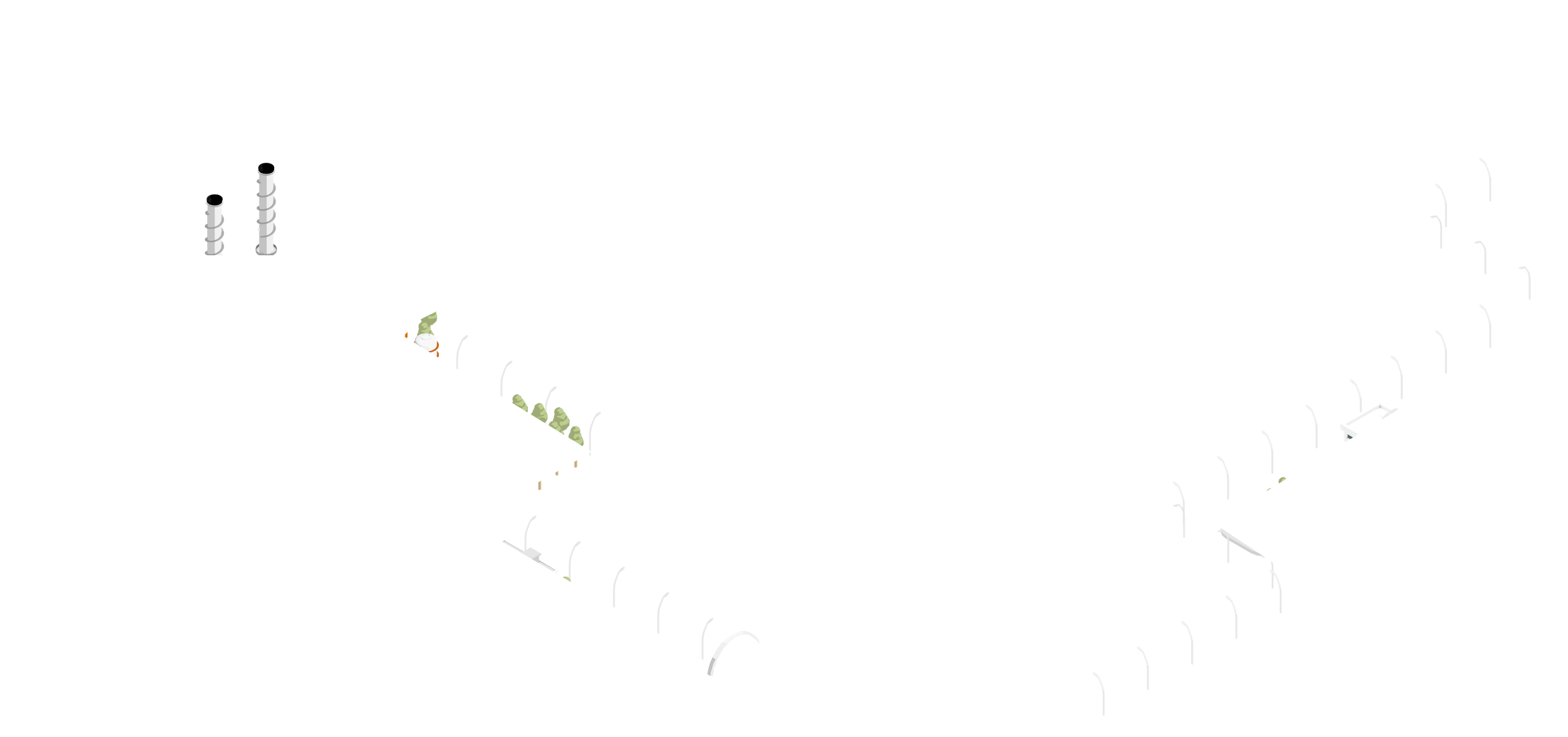
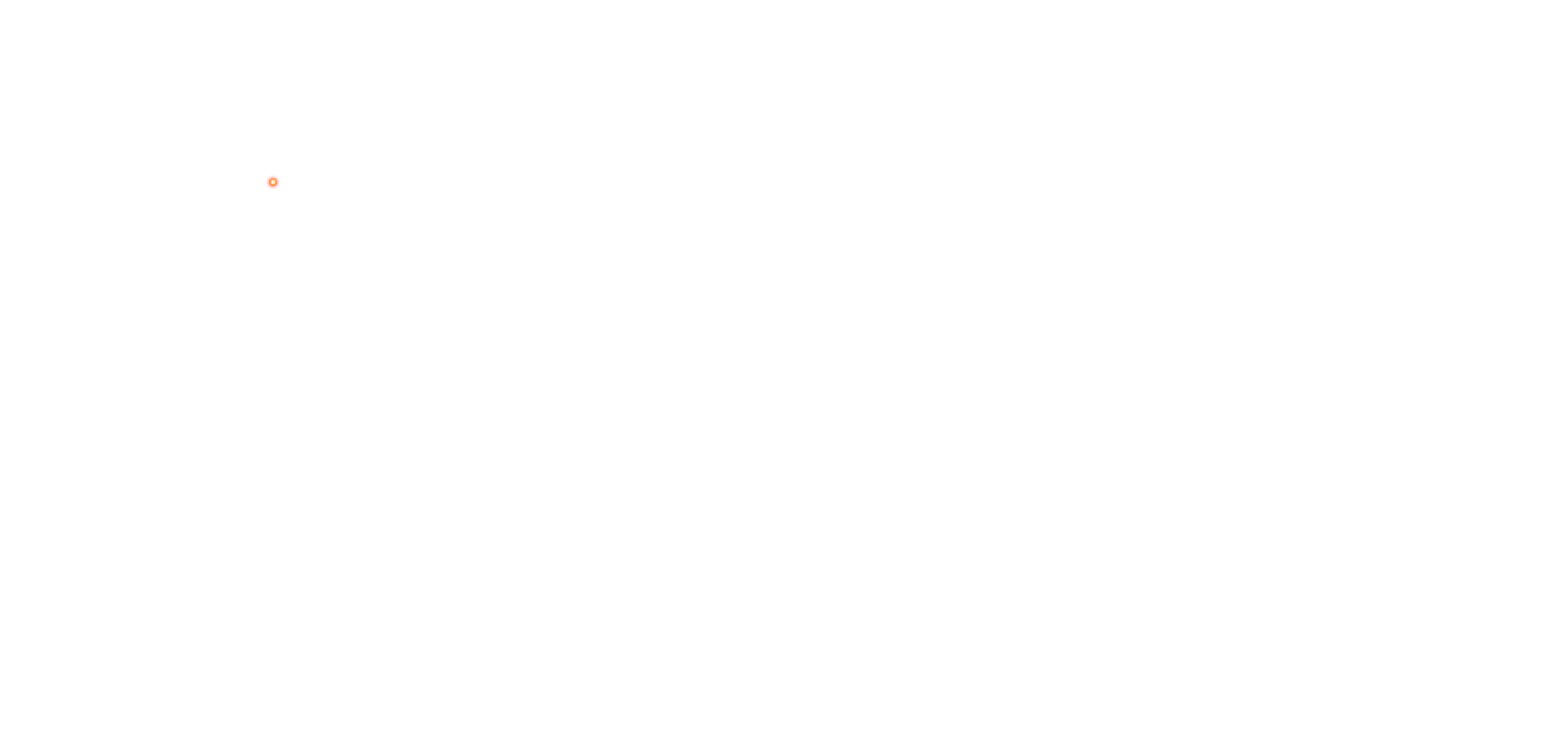
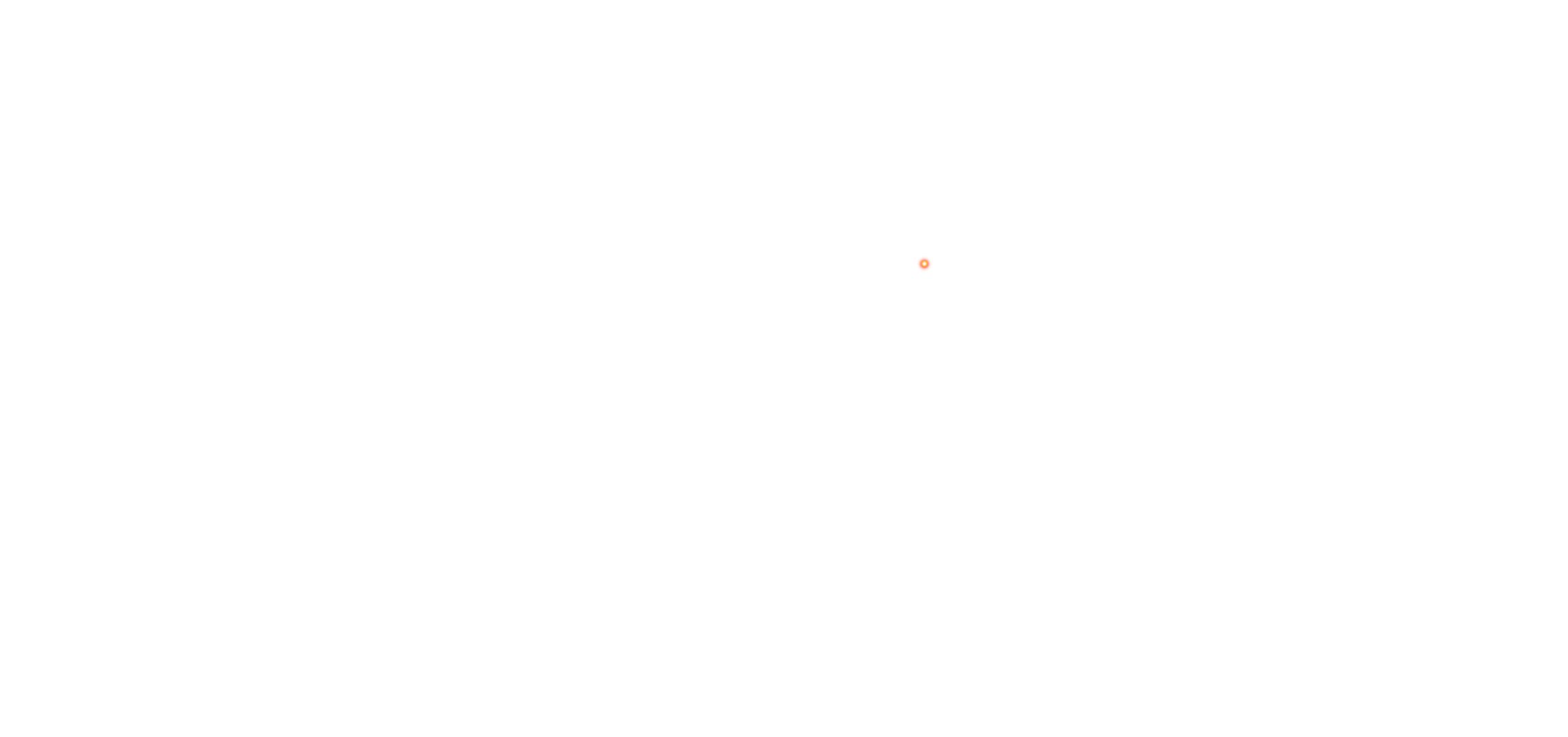
Nuestras instalaciones
El Complejo Industrial se emplaza entre los municipios de A Coruña y Arteixo.
Está ubicado en dos valles (Nostián y Bens) y ocupa una extensión de 150 hectáreas en total, aunque empezó siendo sólo de 70.
También contamos con dos terminales marítimos en donde los barcos cargados de crudo atracan y se llevan los productos ya elaborados. Estos están situados en el Puerto Interior de A Coruña y el Puerto Exterior de Langosteira (Arteixo). Ambas instalaciones están unidas al Complejo Industrial mediante dos oleoductos.
Ubicada en el valle de Nostián en ella se sitúan las unidades de conversión que son aquellas que permiten volver a procesar fracciones pesadas de menor valor obtenidas en los procesos de destilación de crudo y conseguir productos destilados con mayor valor añadido. Es una de las principales características de la refinería de A Coruña, que posee un alto índice de conversión.
Ubicada en el valle de Bens está dividida en combustibles 1 y 2. La capacidad máxima de destilación de crudos de la refinería es de 6.000.000 Tm/año.
En nuestro terminal marítimo, que actualmente está operativo en el Puerto interior de A Coruña, atracan los buques que traen crudo a la refinería y otros que se llevan productos ya elaborados para su comercialización.
El terminal cuenta con 4 pantalanes de atraque de barcos hasta una capacidad máxima de 120.000 toneladas para carga y descarga. Además, cuenta con un parque de almacenamiento con tanques para productos ya elaborados.
Las instalaciones de terminal marítimo se unen a la refinería a través de un oleoducto de 6,5 Km, formado por 14 tuberías de distinto diámetro preparadas para la conducción de diferentes productos.
En las plantas de blending de gasolinas, de gasoil y de fuel oil se mezclan las corrientes provenientes de las distintas unidades de Combustibles y de Conversión para fabricar los distintos productos finales que se comercializan en el complejo industrial.
El blending está compuesto por un complejo conjunto de tuberías, mezcladores, caudalímetros, tanques y procedimientos de control en el que se van añadiendo los aditivos y componentes necesarios para optimizar el blending de los productos finales.
En el área de tanques de almacenamiento de productos se almacena el crudo que llega a la refinería hasta que se procesa en las distintas unidades. Previamente se elimina el agua que pudiera contener el crudo y se mantiene a la temperatura óptima para controlar su viscosidad. Además, también hay tanques que almacenan los productos intermedios y los productos finales.
El número de tanques y esferas (contienen LPG’s en estado líquido como el butano, propano y propileno) instalados en la refinería y el terminal marítimo es de 109.
En nuestras dos unidades de destilación atmosférica, primero se realiza la eliminación de sales del crudo y posteriormente se calienta el crudo en un horno para entrar después en la torre de destilación atmosférica. Es aquí donde el crudo se fracciona en diferentes productos a partir de su punto de ebullición. Los componentes más ligeros ascienden hasta la parte superior de la torre, mientras que los más pesados acumulan en el segmento inferior.
Aquí obtenemos numerosos productos, fuel gas, GLP (Gases Licuados del petróleo), nafta ligera, nafta pesada, queroseno, diésel, gasoil pesado y un residuo atmosférico, que es la parte del crudo que no llega a fraccionarse en esta primera destilación.
Las antorchas son uno de nuestros principales sistemas de seguridad. Siempre mantienen una pequeña llama para estar preparadas para quemar, en caso necesario, hidrocarburos procedentes de las diferentes Unidades en caso de parada de las mismas por alguna incidencia operativa.
Más información
En nuestras tres unidades de destilación a vacío se trata el residuo atmosférico resultante del proceso de destilación atmosférica, sometiéndolo a una segunda destilación a muy baja presión, en condiciones de vacío.
En este proceso obtenemos gasoil de vacío, que se utilizará como alimentación a la unidad de FCC, y un residuo de vacío que servirá para alimentar la planta de Coquer, para producir asfaltos o producir fuel oil, dependiendo del crudo que se procese y la demanda de los distintos productos.
El residuo de las unidades de vacío se procesa en la unidad de coquización retardada donde las moléculas de hidrocarburo se someten a un proceso conocido como craqueo térmico. Así, este residuo de vacío se transforma en gases, naftas, gasoil ligero y pesado que se emplean en la fabricación de gasolinas, gasoil, y como diluyentes de fueloil. Adicionalmente y como producto final se produce coque verde de distintas calidades. La capacidad de procesamiento de esta Unidad es de 1.080.000 Tm/año.
La refinería suministra el propano y el butano a la planta de Repsol Comercial, y cuenta con sus propios depósitos y esferas de almacenamiento. La mayoría de la producción de ambos productos se destina a esta planta, para la demanda nacional. Se embotella tanto para Repsol, que es mayoritario, como también para otros distribuidores.
Las salas de control son el centro neurálgico desde el que se controlan todos los procesos de la refinería. Los operadores de panel de las salas de control cuentan con unas pantallas con esquemas de las unidades desde donde se supervisan variables como la presión, la temperatura, los niveles, los caudales o los analizadores en línea, todo ello en tiempo real. Adicionalmente en las pantallas, el operador de panel puede recibir avisos de cualquier variable de los procesos.
En el complejo industrial de A Coruña contamos con dos salas de control que gracias a las últimas tecnologías permiten al personal de Repsol manejar los procesos de forma digital desde consolas con software y hardware propios.
En esta unidad se reduce el azufre (hidrodesulfuración) del gasoil de vacío y de otros gasóleos pesados mediante una reacción química con hidrógeno para que después puedan pasar a la planta de FCC. El azufre extraído en fase gas (SH2) se convierte en azufre comercial en las unidades de PRA (Planta de Recuperación de Azufre), lo que permite su comercialización como producto final, que es de gran utilidad en la industria agraria y en la fabricación de neumáticos más seguros.
Las denominadas HDS1 y HDS2 se emplean para reducir el azufre de los gasoleos medios obtenidos en las unidades de destilación atmosférica hasta el nivel requerido para producir los gasóleos comerciales (gasoil de automoción, gasoil agrícola y gasoil de calefacción), mediante un proceso de hidrogenación catalítica. Su capacidad es de 2.150.000 Tm/año.
En estas unidades también se realiza el procesado de aceite vegetal y aceite usado de cocina para producir BIOS que se incorporan a la mezcla de gasóleos.
Desde nuestro parque eléctrico nos conectamos con la red externa para importar y exporta la electricidad generada desde las plantas de Cogeneración según corresponda, y es que nuestro complejo además de autoabastecerse también sirve energía a la red nacional.
Las oficinas del complejo industrial albergan a los empleados que se encargan de tareas corporativas como Administración, Compras y Contrataciones, Comunicación, Economía y Finanzas, Planificación, Organización y Servicios, Recursos Humanos, y Servicios de Prevención. En ellas los empleados de Sistemas, Procesos, Ingeniería y Programación y Control de la Producción también realizan tareas de soporte a la operación.
En el laboratorio se analiza la calidad de la materia prima que recibimos y garantizamos que nuestros productos cumplan los más estrictos estándares de calidad, y que nuestros procesos sean seguros y respetuosos con el medio ambiente.
En sus instalaciones realizamos un análisis de muestras cada 5 minutos, para lo que se utilizan las mejores técnicas y equipos disponibles en el sector. En A Coruña, anualmente realizamos: 60.000 muestras, 160.000 análisis, 1.400 certificaciones de calidad y 5.000 calibraciones.
El producto necesario para la producción de asfaltos se obtiene en el fondo de la torre de destilación a vacío, donde se acumulan los componentes más pesados el crudo. Al mezclarlo con grava, se utiliza para crear el pavimento de las carreteras.
En la refinería de A Coruña existe un cargadero destinado a asfaltos con 4 isletas de carga desde donde se cargan 3 calidades diferentes de asfalto. Desde el cargadero también se realiza la carga de buques para asfalto de exportación.
En este parque se encuentran los recursos humanos y materiales necesarios para garantizar la máxima seguridad de las personas, las instalaciones y el entorno en caso de incidentes. Disponemos de un equipo permanente de operadores de seguridad, además de medios técnicos, como equipos y vehículos de última generación, para una respuesta rápida en emergencias. Además, cooperamos con el Parque de Bomberos de A Coruña tanto a través de los equipos humanos y medios materiales, como a través del intercambio de información sobre métodos de lucha contra emergencias.
Más información
La cogeneración alberga las unidades donde generamos energía eléctrica y parte del vapor necesario que necesitamos para nuestro funcionamiento, utilizando como alimentación Gas Natural. En el complejo industrial de A Coruña, contamos con dos plantas de cogeneración que suman una potencia conjunta cercana a los 80 MW hora de potencia eléctrica, suficiente para autoabastecernos y exportar a la red nacional.
A través de nuestras seis chimeneas expulsamos de forma segura y controlada los humos de combustión de los hornos de proceso. Las chimeneas poseen analizadores y están monitorizadas en todo momento para medir las emisiones de forma continua. Estos datos se envían a las autoridades medioambientales pertinentes.
Las aguas procedentes de los distintos procesos se someten a tratamiento primario (separación de aceite mediante API’s), secundario (Tratamiento físico-químico con separación por flotación) y terciario (tratamiento biológico), logrando que el agua tratada pueda recircularse en la refinería para los distintos procesos. De esta forma, reducimos al máximo nuestro consumo externo de agua, optimizamos el uso de los recursos naturales y somos respetuosos con el medio ambiente. La capacidad de esta planta es de 7.000.000 m3/año.
Los gases procedentes de Conversión sufren un proceso de compresión y absorción para recuperar GLP y pequeñas fracciones de nafta ligera, obteniéndose propano, butano y gasolina de bajo número de octano. Adicionalmente se separa el fuel gas que se utiliza como combustible a nuestros hornos de proceso. En el área de Combustibles se localiza otra unidad de recuperación de gases cuya función es similar.
El residuo de las unidades de vacío se procesa en la unidad de coquización retardada donde las moléculas de hidrocarburo se someten a un proceso conocido como craqueo térmico. Así, este residuo de vacío se transforma en gases, naftas, gasoil ligero y pesado que se emplean en la fabricación de gasolinas, gasoil, y como diluyentes de fueloil. Adicionalmente y como producto final se produce coque verde de distintas calidades. La capacidad de procesamiento de esta Unidad es de 1.080.000 Tm/año.
El cargadero de fuelóleo cuenta con con 4 brazos de carga para suministrar al hinterland. Adicionalmente se comercializa IFO 0,5 % S (combustible marítimo) que se carga a buques a través del oleoducto.
El propano olefínico procedente de las unidades de Conversión se destila en una torre con alto grado de fraccionamiento, separándose en propano y propileno grado polímero, que es alimentación de las empresas petroquímicas y tiene múltiples utilidades en el uso diario. La capacidad de producción de propileno grado polímero es de 81.000 Tm/año.
Más información
En la refinería podemos encontrar bios en gasolinas y en gasóleos.
Los bios en gasolina provienen del bioetanol obtenido de recursos renovables que se incorpora del exterior del complejo industrial y junto con el butano olefinico procedente de las unidades de Conversión alimenta a la Unidad de ETBE para obtener ETBE producto que es componente bio del blending de gasolinas.
Los bios en gasóleos provienen de la incorporación de aceite vegetal (VO) y aceite de cocina usado (UCO) del exterior que se coprocesa en nuestra Unidad de HDS-2 y se incorpora al gasoil de automoción.
Los bios en gasóleos también provienen de la incorporación del exterior de éster metílico de ácidos grasos (FAME, biocombustible producido por la transesterificación de aceites vegetales) y de aceite vegetal hidrotratado (HVO). El FAME y el HVO, sin entrar al proceso de ninguna unidad, se incorpora al blending de gasoil como componentes bio.
Desde 2015 estamos operando los productos sólidos (azufre y coque) en el Puerto Exterior de A Coruña, situado en Punta Langosteira. Actualmente estamos desarrollando un proyecto de traslado de las operaciones de crudo desde el Puerto interior de A Coruña al exterior de Langosteira con una inversión de 126 millones de euros. Si quieres saber más del proyecto
Más información
La refinería cuenta con una unidad propia en la que se produce hidrógeno, a partir del reformado de gas natural o butano para su utilización en las unidades de hidrodesulfuración. Su capacidad de producción es de 10.000 Tm/año. Además, existe una planta externa, propiedad de Air Liquide que suministra a la refinería el hidrógeno necesario para su utilización en la unidad de HDT, o de las otras, en caso de parada de nuestra planta de hidrógeno.
En estas unidades, la nafta pesada obtenida por la destilación se somete a un proceso catalítico de lecho fijo y se obtiene una gasolina de alto número de octano, que se usa para producir por blending (mezcla), las gasolinas comerciales de 95 y 98 octanos.
Las paradas programadas
Nuestras instalaciones funcionan 24 horas, todos los días del año.
El mantenimiento de nuestras plantas es una actividad que realizamos de forma diaria, pero periódicamente tenemos que realizar trabajos de revisión, renovación e inspección para incorporar tecnologías más avanzadas o inversiones de mejora.
Estos trabajos de mantenimiento sólo pueden llevarse a cabo con las unidades fuera de servicio y los denominamos paradas programadas.
Nuevo terminal marítimo en el Puerto Exterior
Conoce el proceso de traslado gradual de nuestras operaciones de sólidos y crudo a Punta Langosteira (Arteixo).
Un proyecto que ha supuesto una inversión de más de 126 millones de euros.
Otras inversiones
La nueva unidad de obtención de propileno grado polímero permite mejorar la competitividad y eficiencia del Complejo Industrial de A Coruña, uno de los principales motores de la economía coruñesa y gallega.
Repsol Química
Los productos que fabricamos y comercializamos te ayudan a mejorar tu día a día.
Proceso productivo
Gracias a la I+D+i y a la experiencia de más de medio siglo investigando, A Coruña se ha convertido en el moderno complejo industrial que es hoy.